Programação e Manutenção: A Sinergia Entre APS e TPM
Pensando na teoria, a gestão de manutenção e a programação da produção parecem ser processos muito íntimos e interligados, afinal eles gerenciam muitos recursos em comum e possuem os mesmos objetivos de aumentar a disponibilidade e a eficiência dos mesmos. Porém, a integração entre eles é pouco explorada na prática atual da indústria brasileira. E eu compreendo: ambas as áreas possuem recursos de pessoas bem enxutos e uma visibilidade futura baixa, com muita incerteza, o que faz com que, infelizmente, a gestão precise ser o mais simples possível, focando no que é mais crítico, urgente e conhecido.A LIMITAÇÃO PELA BAIXA VISIBILIDADE Quem trabalha com a TPM (Total Productive Maintenance, ou Manutenção Produtiva Total) já possui uma base mais sólida para uma ação conjunta com o PPCP pois dentro dos seus pilares estão as manutenções planejadas, sejam elas preventivas ou preditivas. Contudo, esse planejamento é realizado e normalmente fica dentro da área de Manutenção e a informação dificilmente chega ao PPCP de uma maneira formal. A informação vem em um telefonema, numa reunião, ou numa conversa de corredor, quando as áreas interagem e a manutenção informa “Olha, PPCP, a máquina X vai ter uma manutenção de 4 horas nessa próxima quinta-feira às 14h.”Essa situação é agravada para quem não utiliza um software APS, pois mesmo que o plano de manutenções tenha um horizonte maior do que uma semana, o próprio PPCP não tem como enxergar mais do que poucos dias na sua própria programação de produção com precisão. Então a manutenção que está mais adiante não tem um uso claro. Enfim, esse cenário de baixa visibilidade e acuracidade de programação limita a sinergia entre as áreas.Por outro lado, quando temos uma programação de produção através do APS, conseguimos aprimorar estes processos.APS + TPM PARA PLANEJAMENTOQuando se inicia o uso do Opcenter APS, um ponto bem interessante para se enxergar a capacidade finita de produção é trazer as manutenções planejadas para o gráfico de Gantt, para que elas já sejam consideradas no momento de programar, como na imagem abaixo. Assim, uma operação não consegue ser programada nesse momento em um recurso que já estará comprometido com uma manutenção.
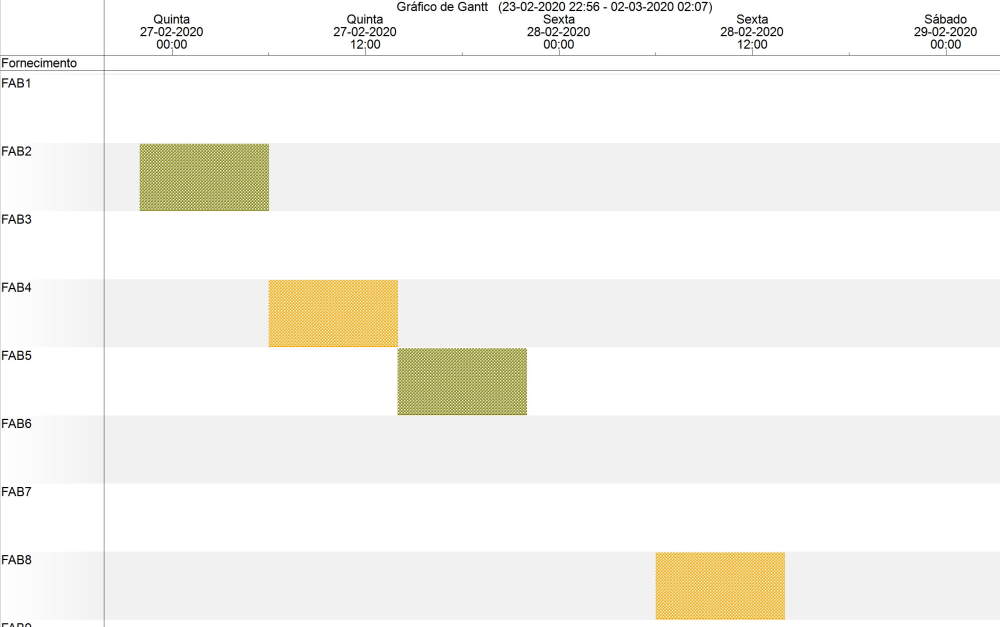
Figura 1 - Gantt pré-programação com manutenções preditivas em verde e preventivas em laranja
Essas manutenções podem ser registradas diretamente pelo usuário-chave do Opcenter APS, porém o ideal é que elas possam ser importadas de outro sistema, seja o módulo de manutenção do seu ERP, MES ou de um sistema especialista de manutenção.Um próximo passo de sinergia pode surgir quando as manutenções não precisam ocorrer exatamente naquele dia e horário específicos, mas sim, em um determinado período ideal. Assim, pode-se realizar a alocação exata da manutenção após o PPCP analisar a programação da produção em si. Por exemplo, um software de manutenção preditiva pode informar ao APS quando serão as manutenções e já fixá-las no horizonte como mostra a Figura 1, porém também poderia criar uma requisição de manutenção para ser alocada em um determinado período, e que teria seu dia e hora exatos alocados pelo PPCP no APS, respeitando os limites indicados pela manutenção e enxergando qual é o melhor momento para que essa manutenção ocorra prejudicando o mínimo possível a produção.Devido ao fato do sincronismo entre as operações e os turnos de cada recurso serem considerados no APS, torna-se possível visualizar situações em que uma manutenção alocada no turno da manhã ou da tarde altera a eficiência produtiva. Inclusive esse impacto na eficiência pode ocorrer não somente para o recurso que sofrerá a manutenção, mas também para as operações posteriores que dependem da produção daquele recurso. Ou seja, a conversa entre o que a manutenção precisa e o que o PPCP necessita através de uma programação integrada potencializa ganhos de eficiência.É claro que realizar essa mudança não é simples, você precisa ter um processo bem estruturado, com responsáveis e prazos para estas novas atividades, assim como é necessário adicionar mais camadas de integração entre os sistemas, pois o APS devolverá as datas programadas das manutenções também. Ainda assim, os ganhos de eficiência e melhor visibilidade favorecem a iniciativa.
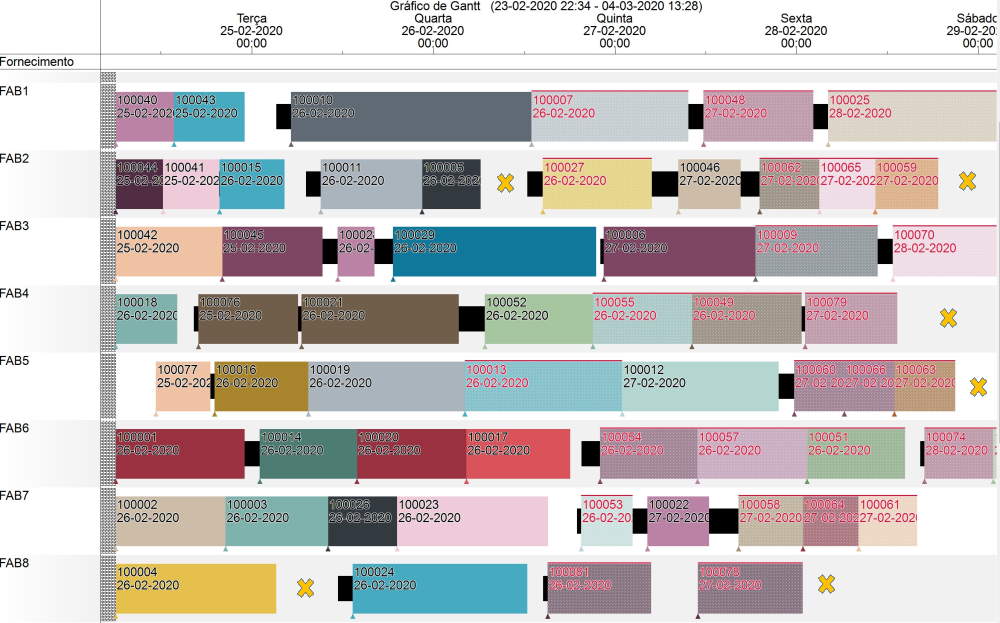

Potenciais lacunas para encaixe de manutenção
Figura 2 – Gantt pós-programação com lacunas potenciais para alocação de manutenções
MAS E AS MANUTENÇÕES CORRETIVAS?As manutenções corretivas talvez sejam as mais críticas para serem contempladas numa integração entre o APS e o EPR ou MES, dada a urgência de agilidade na resposta que o PPCP precisa ter quando um imprevisto como uma quebra de máquina ocorre e o impacto que o problema pode gerar.Porém, justamente devido à urgência e à escassez de recursos para padronizar processos, muitas indústrias resolvem esses problemas fora de sistema. Primeiro, isso é um problema para a própria manutenção pois não se registra histórico de paradas e prejudica indicadores como o MTBF (Mean Time Between Failures) e o MTTR (Mean Time to Repair). Segundo, se isso não entrar em sistema, o APS dependerá de uma intervenção manual do programador para inserir a manutenção corretiva e realizar a reprogramação da produção a partir disso. Esse processo manual é viável, porém perde agilidade.Uma boa integração entre o ERP ou MES com o APS permite que, ao ocorrer um evento de manutenção corretiva, o APS possa já bloquear o recurso durante o tempo previsto para diagnóstico, o MTTD (Mean Time To Detect), assim como atualizar a duração da manutenção de acordo com o MTTR previsto para aquele tipo de problema, uma vez que ele foi diagnosticado.
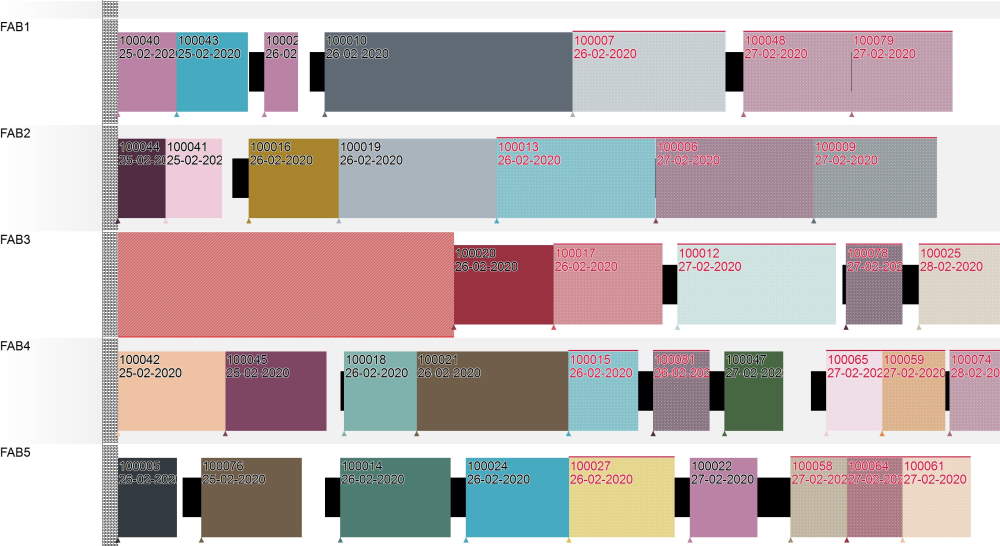
Figura 3 – Gantt com programação e manutenção corretiva em vermelho com tempo automaticamente importado pelo MTTR
É importante entender que paradas muito curtas provavelmente não impactem a programação da produção (nem a reprogramação), pois são eventos de curtíssimo prazo e sem expressão suficiente (o impacto desses problemas pode ser medido através da aderência à programação). Porém, paradas maiores ou em recursos extremamente críticos podem exigir uma resposta sob demanda imediata e essa integração ágil pode tornar-se um grande diferencial.Então, gostou do conteúdo?
E como a NEO pode ajudar a sua indústria?
A NEO Engenharia de Produção é Siemens Smart Expert Partner e oferece soluções com análise de negócio e implementação dos softwares APS. Criamos um novo conceito que valoriza a vanguarda tecnológica e a excelência técnica, ao mesmo tempo em que acreditamos na sensibilidade humana, no trabalho criativo e no relacionamento personalizado e comprometido.Entre em contato pelo formulário abaixo ou pelo nosso WhatsApp para saber mais sobre as nossas soluções e marcar uma análise personalizada para as necessidades do seu negócio.Realize o sequenciamento da sua produção com quem é especialista em soluções tecnológicas.